|
Anti-roll
suspension
|
Between
February 1955 - barely six months after the launch
of the DS
-
and November 1968, six DS were successively fitted
with anti-roll
suspension systems and covered more than 6 000
km. The studies
were intended to improve on both comfort and
roadholding (neither of
which could hardly be called bad!) compared to the
production car. |
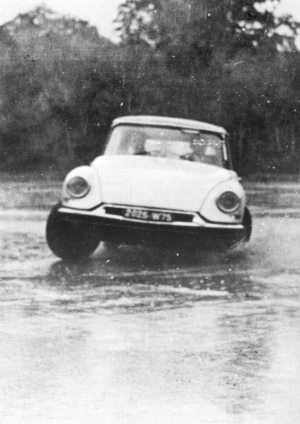 |
|
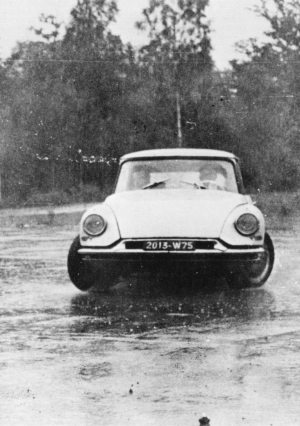 |
The
two pictures above demonstrate the system in
action - the car on the
left is a normal production vehicle, the one on
the right is fitted
with antiroll - same bend, same speed. The
picture on the right
gives little indication of the speed - until you
notice how the left
front tyre is deformed.
The
system could have been put into production in
the late sixties but the
team was forced to abandon its research to
concentrate on the
soon-to-be launched GS.
A prototype
SM with
zero roll suspension was also developed in 1973.
Paul
Magès had intended such a system to be part of
the design of the
suspension system and as early as 1944, he had
sketched just such a
system, a derivation of which was fitted to a prototype 2CV
in 1946.
|
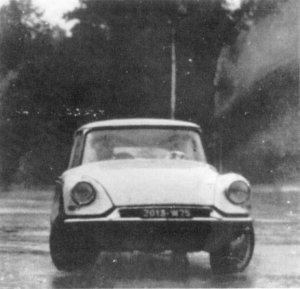 |
It was not
until the launch of the Xantia
Activa
below that such a system was put into
production
 |
ELECTRONIC
DATA
1 Steering wheel angle
2 Rate of steering wheel rotation
3 Vehicle velocity
A High pressure pump
B Anti roll regulator
C Electro valve
D Regulator
E Activa accumulator
F Front stabiliser cylinder
G Rear stabiliser cylinder
H Stabiliser
I Suspension computer
|
 |
FRONT
SUSPENSION
MECHANICAL LAYOUT
1. Front stabiliser bar
2. Front stabiliser (anti-roll) bar
|
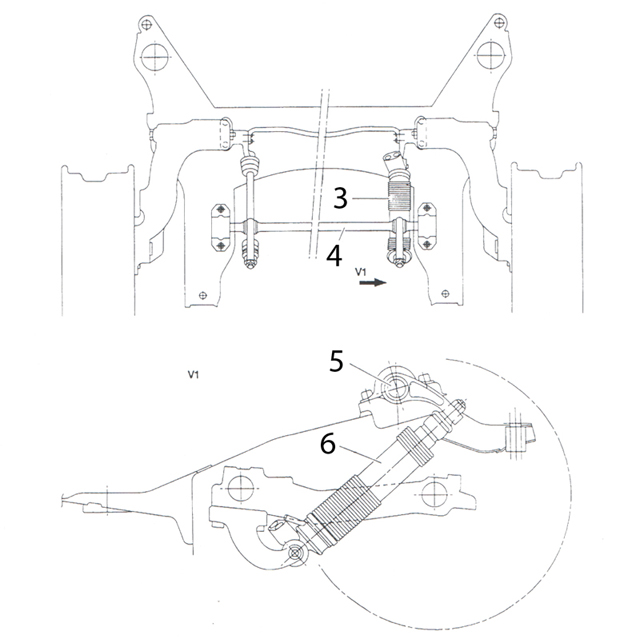 |
REAR
SUSPENSION
MECHANICAL LAYOUT
3. Rear stabiliser cylinder
(hydraulic ram)
4. Rear stabiliser (anti-roll) bar
5. Rear stabiliser (anti-roll) bar
6. Rear stabiliser cylinder
(hydraulic ram)
|
|
Other
developments
|
|
|
Electro-hydraulic
gearbox
Anti-roll
suspension was not the only project
being developed by Paul Magès'
team. Amongst the ideas being
contemplated were electro-hydraulic
control of the gearbox which employed
electronics to change gear,
making use of the following parameters:
vehicle speed, engine speed,
throttle depression and rate of throttle
movement. The result was
an improvement of 10% in economy and
improved performance. This
project never made it into production. |
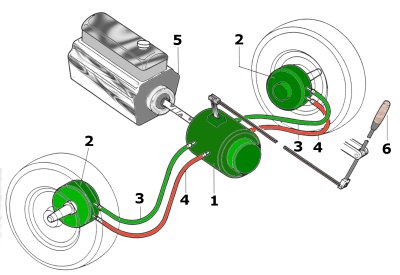 |
Hydrostatic
transmission
Hydrostatic
transmission was yet another idea that
was abandoned. As early
as1908, Louis Renault had proposed just
such a system. The idea
is relatively simple; the engine drives
a pump which sends fluid under
pressure to four hydraulic pumps in each
wheel hub. There is no
need for different gear ratios and
transmission is therefore
continuous, the clutch being dispensed
with also. Furthermore
there was no need for a separate braking
system. Magès and his
colleagues worked on this project for
twenty eight years and some
thirty prototypes were fitted with the
system (2 CVs, GSs and a CX)
between 1958 and 1973 and covered a
total distance of 1 130 000
km. However there were major
problems with noise and when Peugeot
took control in 1974, the project was
killed off. Hydrostatic
transmissions are used in vehicles such
as forklift trucks and some
specialist earth moving vehicles. |
1.
hydraulic
pump
2. hydraulic motors
3. hydraulic pipes - forward
rotation
4. hydraulic pipes -
backwards rotation
5. conventional engine |
Joystick
steering
Magès
also worked on the project that led to
the DIRAVI steering system -
powered return of the wheel to the
straight ahead position coupled with
both variable ratio (movements around
the straight ahead position
result in small deflections while moving
away from this position
results in larger deflections) and
variable assistance (as velocity
increases, assistance diminishes).
A DS was fitted with a system
which was 100% assisted and the steering
wheel was replaced with an
aircraft type joystick - one steered
with tiny movements of a finger
and with one's eyes. It was felt
that despite the undoubted
advantages such a system would offer
(unrestricted view ofthe
instrument panel and removal of the
injury potential of a wheel and
column), the clients would dislike it. |
Hydraulic
motors
Hydraulic
motors weigh one sixth of an equivalent
electric motor. Since the
DS was already fitted with a high
pressure hydraulic system, it was
logical to look at other applications
including an hydraulically
powered cooling fan
(30% reduction in weight and 30%
reduction in radiator volume, thereby
freeing up some much needed under bonnet
space and allowing the
radiator to be mounted at an angle); hydraulically
powered
windscreen wipers which had much
higher starting torque than
electric ones and could be steplessly
variable in speed; an hydraulically
powered alternator which would
supply power on demand; hydraulically
powered
window lifters, hydraulically
powered starter motor... |
|
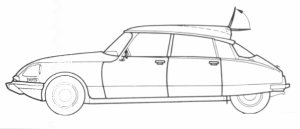 |
|
...and probably most
bizarre of all, a roof mounted, hydraulically
powered air brake which
not only employed wind resistance to slow the car
but also increased
the rear wheel downforce thereby reducing the
tendency for the rear
brakes to lock up. As early as the beginning
of the sixties, an anti-lock
braking system had also been perfected. |
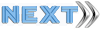 |
|
©1999 Julian Marsh |